Understanding Hydraulic Balls: Applications and Benefits
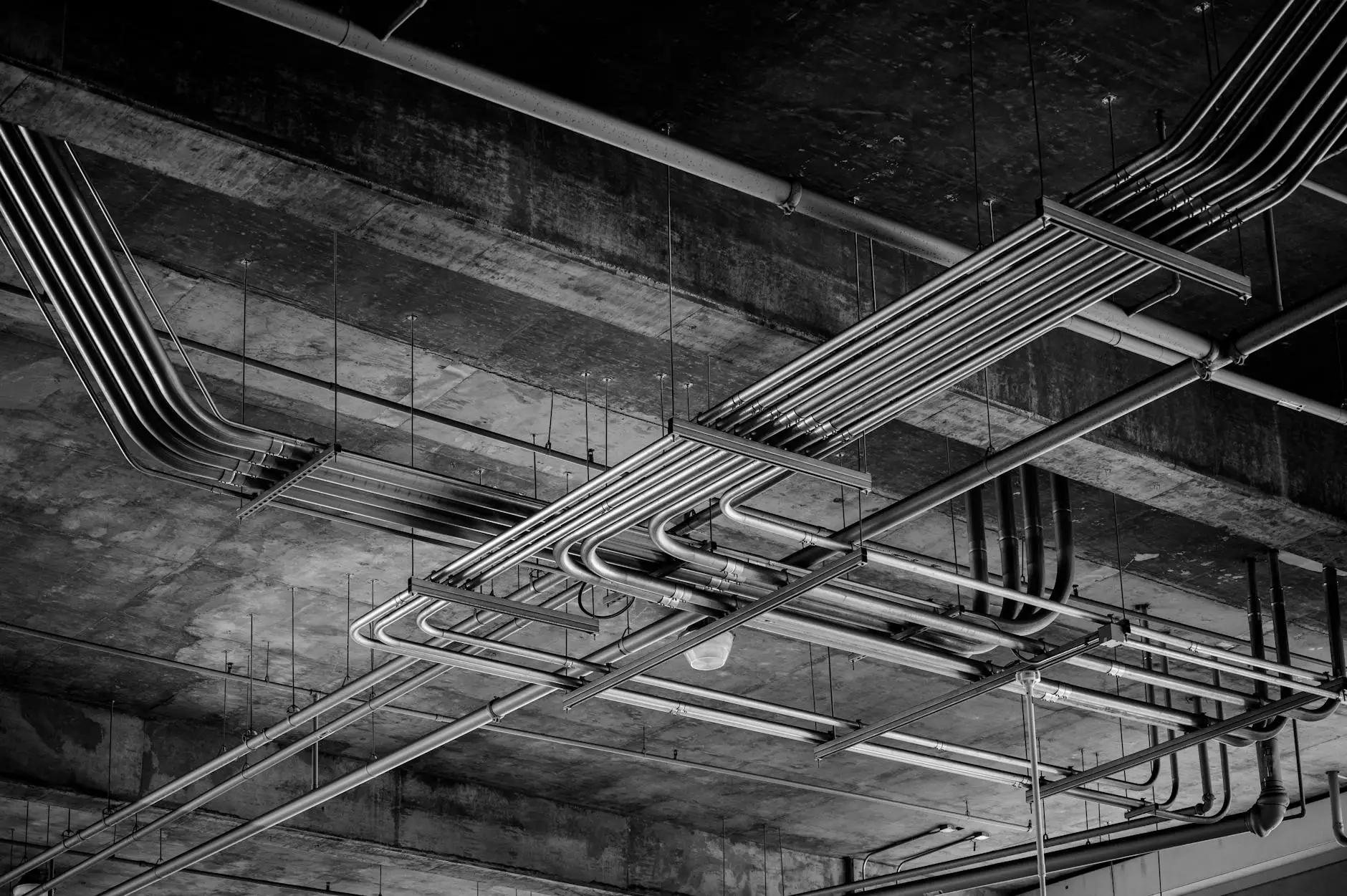
In the world of fluid mechanics and control, hydraulic balls play an integral role in various applications. These devices are designed to manage the flow of fluids with precision, ensuring efficiency and safety in operations across multiple industries, including manufacturing, automotive, and aerospace.
What are Hydraulic Balls?
Hydraulic balls are spherical devices that facilitate the control and regulation of fluid flow in hydraulic systems. They are commonly used in ball valves, which act as on-off switches for fluid flow. Their rounded design allows for minimal resistance when fluid passes through, making them highly effective in managing hydraulic pressures.
The Structure of Hydraulic Balls
The design of a hydraulic ball is crucial for its performance and longevity. Typically made from materials such as stainless steel, brass, or plastic, these balls must withstand high pressures and corrosive environments. The following features highlight the essential elements of hydraulic balls:
- Material Quality: High-quality materials ensure durability and resistance to wear and tear.
- Precision Engineering: Hydraulic balls must be engineered to exact specifications to ensure a perfect fit within the valve housing.
- Surface Finish: A smooth surface finish reduces friction and enhances the flow characteristics of fluids passing over the ball.
Types of Hydraulic Balls
There are several types of hydraulic balls that cater to various industrial needs:
- Floating Balls: These are not fixed in place and move slightly to create a seal against the valve seat.
- Trunnion-Mounted Balls: These balls are fixed at their top and bottom, providing greater stability and controlling higher flow rates.
- Metal-Seated Balls: Ideal for high-temperature applications due to their ability to withstand extreme conditions without deformation.
- Soft-Seated Balls: These are made with a softer seat, providing a tighter seal and minimizing leaks in lower pressure systems.
The Role of Hydraulic Balls in Fluid Control
The primary function of hydraulic balls is to act as a control mechanism for liquids and gases. In hydraulic systems, these balls provide several benefits:
1. Efficient Fluid Regulation
By using hydraulic balls, systems can achieve precise control over the flow rate of fluids. This efficiency is crucial in processes where accurate amounts of fluid are necessary for operational success.
2. Enhanced Safety
The reliable shut-off capability of hydraulic balls prevents fluid leaks that can lead to hazardous situations. Industries that handle flammable or toxic fluids particularly benefit from this safety feature.
3. Versatility across Industries
Whether it's in oil and gas exploration, water treatment, or industrial manufacturing, hydraulic balls demonstrate versatility that makes them indispensable across various sectors.
Applications of Hydraulic Balls
The applications of hydraulic balls are as varied as they are important. Here are some key areas where they are extensively utilized:
1. Oil and Gas Industry
In this industry, tightly controlling the flow of fluids is paramount. Hydraulic balls are integral to valves that manage crude oil extraction and transportation, ensuring safe and efficient processing.
2. Water Supply Systems
Water treatment facilities utilize hydraulic balls for flow control in systems that are designed to purify and distribute water. Their ability to maintain pressure and minimize leaks is vital in preserving water quality.
3. Chemical Processing
Chemical plants rely on hydraulic systems to transport corrosive substances safely. The reliability of hydraulic balls in these applications prevents leaks and ensures the effective handling of hazardous materials.
Choosing the Right Hydraulic Ball
Selecting the appropriate hydraulic ball is crucial for optimizing system performance. Consider the following factors:
- Pressure Rating: Ensure the ball can withstand the system's operational pressures.
- Temperature Tolerance: Select materials that can endure the temperature conditions of your application.
- Compatibility with Fluids: Assess the chemical compatibility of the ball material with the fluids being handled.
Maintenance of Hydraulic Balls
Regular maintenance of hydraulic balls is essential to prolong their lifespan and enhance system reliability. Here are some maintenance tips:
1. Regular Inspections
Schedule routine inspections to check for signs of wear, corrosion, or leakage. Early detection of issues can prevent more significant failures.
2. Cleaning Procedures
Keep the hydraulic system clean by removing contaminants that could damage the hydraulic balls or impair their function. Use appropriate cleaning agents that do not compromise material integrity.
3. Lubrication
Ensure that moving parts around the hydraulic ball are adequately lubricated. This reduces friction and helps maintain optimal performance.
The Future of Hydraulic Balls in Technology
As industries evolve, so does the technology surrounding hydraulic balls. Innovative materials and designs are being developed to enhance performance and durability. The future may see advancements like:
- Smart Hydraulic Balls: Integrated sensors that provide real-time data on fluid flow and pressure.
- Eco-Friendly Materials: Development of sustainable materials that reduce environmental impact without compromising performance.
- Increased Customization: Tailored solutions to meet specific operational needs in niche markets.
Conclusion
Hydraulic balls are vital components in modern fluid control systems. Their efficiency, reliability, and versatility make them indispensable across various industries. As technology advances, the potential for enhanced hydraulic ball design and functionality continues to grow, promising even greater benefits for the industry. For businesses looking to purchase quality hydraulic balls and fittings for their operations, exploring offerings from reliable suppliers like fitsch.cn ensures access to the best in the market.