Understanding Injection Moulding Factories
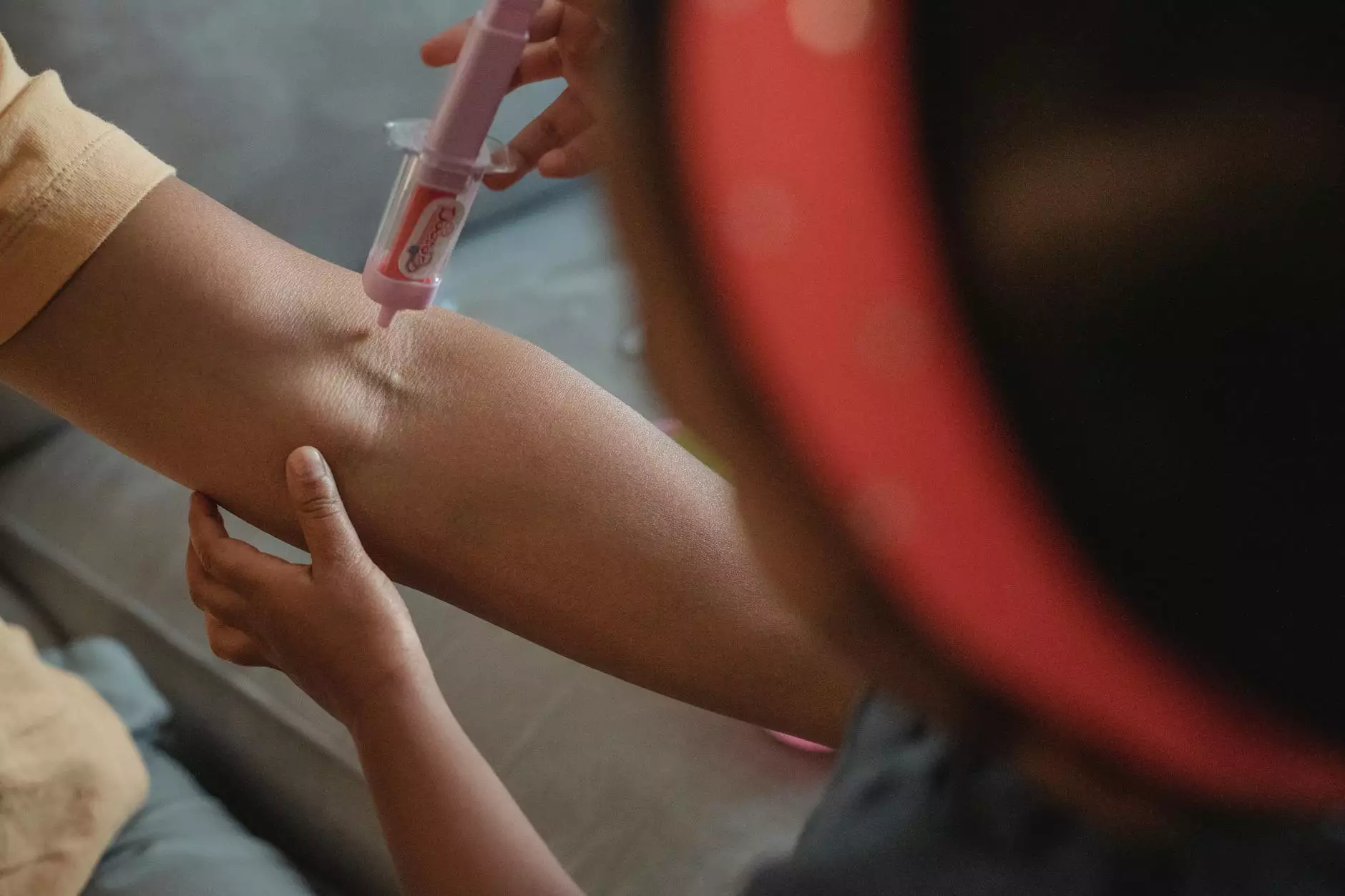
In today's manufacturing landscape, the role of an injection moulding factory is critical. As industries continue to evolve, the demand for efficient, high-quality plastic manufacturing methods has surged. This article aims to provide an in-depth understanding of injection moulding factories, exploring their processes, benefits, challenges, and the contributions they make to various sectors.
What is Injection Moulding?
Injection moulding is a manufacturing process used to produce parts by injecting molten material into a mould. This process is widely utilized for producing items made of plastic but can also accommodate metals and ceramics in some instances. It is favored for its ability to create complex shapes with high precision and repeatability.
The Process of Injection Moulding
The injection moulding process generally involves several key steps:
- Material Selection: Choosing the right material is crucial as it dictates the product's properties and production costs.
- Heating: The material is heated until it becomes molten enough to flow into the mould.
- Injection: The molten material is injected into a pre-designed mould using a screw or a plunger system.
- Cooling: The material begins to cool and solidify inside the mould.
- Ejection: Once cooled, the formed part is ejected from the mould.
- Trimming and Finishing: Any excess material is trimmed and additional finishing processes may be applied.
Types of Injection Moulding
Injection moulding can be categorized into several types, each serving distinct purposes:
- Thermoplastic Injection Moulding: This method uses thermoplastic materials that can be melted and solidified multiple times.
- Thermosetting Injection Moulding: In this case, thermosetting polymers are used which, once set, cannot be remelted.
- Insert Moulding: This technique involves combining different materials into a single part by inserting one material into the mould before injecting the second.
- Multi-material Injection Moulding: This allows for the injection of two or more materials into a single part, providing enhanced properties.
Benefits of Injection Moulding Factories
Injection moulding factories provide numerous advantages, making them a cornerstone of modern manufacturing:
- Efficiency: High production rates allow for mass production, reducing costs per unit.
- Precision and Consistency: The process ensures that each product is made to exact specifications with minimal variance.
- Material Utilization: Injection moulding minimizes waste, as only the exact amount of material needed is used during production.
- Complex Designs: The moulding process can create intricate shapes that would be impossible with other manufacturing methods.
- Reducing Labor Costs: Automation in injection moulding reduces the need for manual labor, further reducing costs.
Applications of Injection Moulding
Injection moulding factories serve a variety of industries. Here are some common applications:
- Automotive: Manufacturing components such as dashboards, panels, and other intricate parts.
- Consumer Goods: Producing everyday items like containers, toys, and household products.
- Medical Devices: Creating precise parts that meet stringent regulatory standards.
- Electronics: Crafting cases and components that require exact tolerances.
Challenges Faced by Injection Moulding Factories
Despite their advantages, injection moulding factories face several challenges that can impact their operations:
- High Initial Costs: The setup costs for moulds can be significant, especially for complex designs.
- Material Limitations: Some materials may not be suitable for the injection moulding process.
- Mould Maintenance: Moulds require regular maintenance and replacement, adding to operational costs.
- Time-Consuming Prototyping: Developing moulds for new products can be a lengthy process.
The Future of Injection Moulding Factories
The future of injection moulding factories is poised for significant advancements as technology evolves. Several trends are shaping the industry's landscape:
- Increased Automation: The rise of smart factories will lead to greater automation, reducing labor costs and improving efficiency.
- Sustainable Practices: There is a growing emphasis on sustainable manufacturing processes, including the use of biodegradable materials and recycling of production waste.
- 3D Printing Integration: Combining 3D printing with injection moulding can enhance the design and prototyping phases, leading to faster and more cost-effective production.
- Customisation: The demand for customised products is increasing, pushing factories to adopt more flexible manufacturing systems.
DeepMould.net: A Leader in Injection Moulding
At DeepMould.net, we pride ourselves on being at the forefront of injection moulding technologies. With years of experience and a dedication to quality, we provide tailored solutions to meet our clients' unique needs. Our state-of-the-art facilities and skilled workforce ensure that we deliver the best products efficiently and reliably.
Why Choose DeepMould.net?
Choosing the right partner for your injection moulding needs is critical. Here are some reasons why DeepMould.net stands out:
- Expertise: Our team consists of industry experts with extensive knowledge in injection moulding.
- Quality Assurance: We adhere to strict quality control measures to ensure that all products meet the highest standards.
- Innovation: We continuously invest in the latest technologies to improve our processes.
- Customer Focus: Our clients are at the heart of our operations. We work closely with you to understand your needs and deliver solutions that exceed expectations.
Conclusion
In conclusion, injection moulding factories are an integral part of the manufacturing ecosystem, driving innovation and efficiency across various industries. As we look to the future, advancements in technology and shifts towards sustainability will shape the evolution of this crucial manufacturing process. Whether you are in the automotive, medical, or consumer goods sector, working with a reliable injection moulding partner, like DeepMould.net, can help you achieve your manufacturing goals with precision and speed.