Understanding the Importance of Precision Plastic Molding in the Metal Fabrication Industry
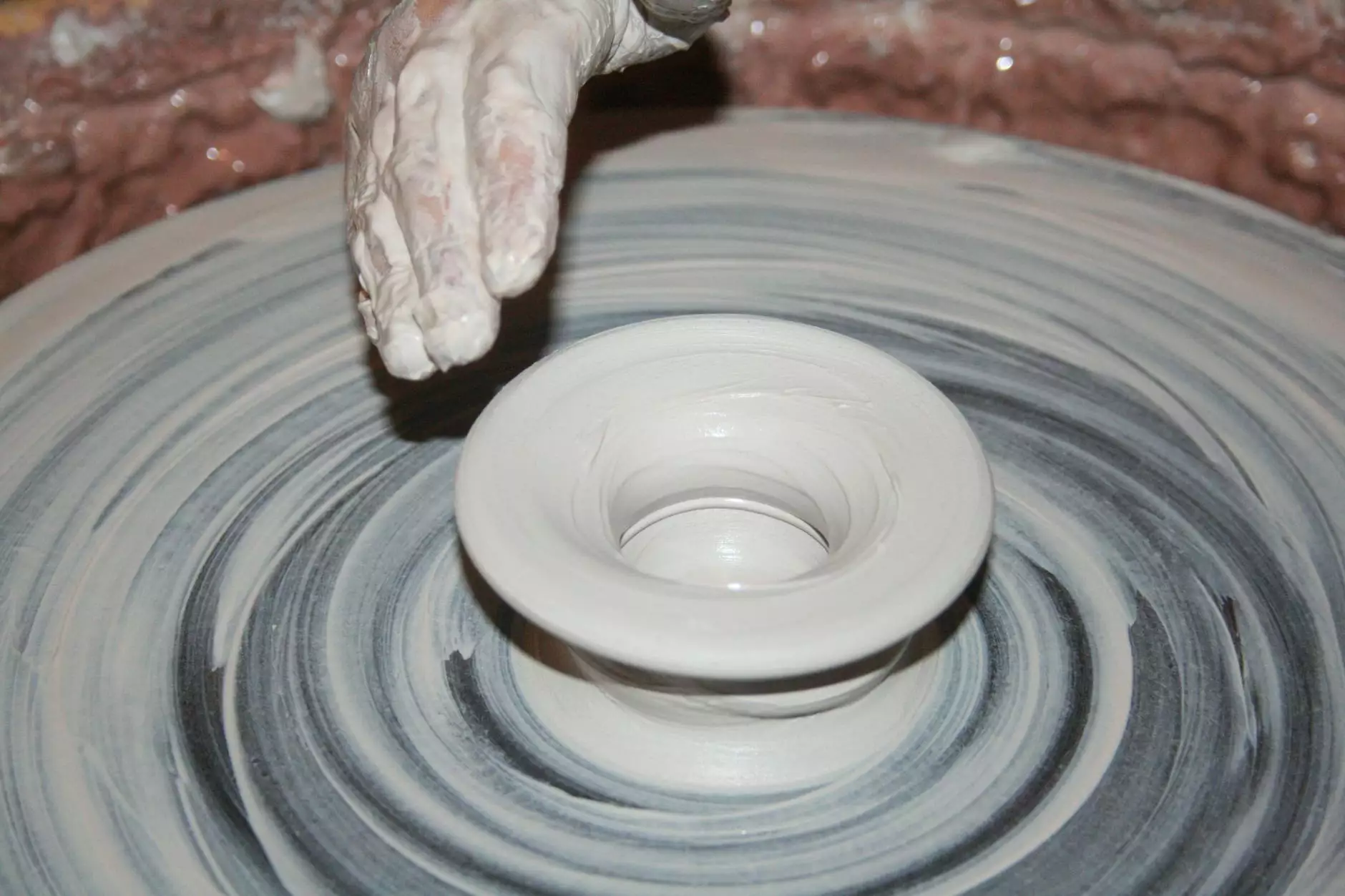
Precision plastic molding has transformed the manufacturing landscape, especially in the field of metal fabrication. As a core technique utilized by businesses like deepmould.net, this method serves to enhance product quality, reduce costs, and streamline production processes.
The Basics of Precision Plastic Molding
At its core, precision plastic molding is a manufacturing process that involves the creation of plastic parts through the use of specialized machinery. The process is characterized by its ability to produce high-quality parts with excellent tolerances and minimal waste. Some key components of precision plastic molding include:
- Injection Molding: A method where molten plastic is injected into a mold cavity.
- Blow Molding: A process primarily used for hollow plastic products.
- Compression Molding: A technique where plastic is heated and molded under pressure.
- Extrusion Molding: A process used to create long plastic materials with a consistent cross-section.
The Role of Precision in Plastic Molding
Precision is crucial in plastic molding, as even the slightest inaccuracies can lead to product failure or increased production costs. Factors contributing to precision in this process include:
- High-Quality Molds: The better the mold, the more accurate the final product.
- Temperature Control: Maintaining precise temperatures can affect the flow and setting of the plastic.
- Material Selection: The type of plastic used can determine the final product's strength and flexibility.
Benefits of Using Precision Plastic Molding
The adoption of precision plastic molding offers numerous benefits to metal fabricators and other industries. Here are some of the most significant advantages:
1. Enhanced Product Quality
With precision plastic molding, businesses can expect a higher level of product quality. The process allows for intricate designs and detailed features that enhance functionality. For instance, companies dealing with metal fabricators can utilize precision molding to create complex components that integrate seamlessly with metal parts.
2. Cost Efficiency
Precision plastic molding is often more cost-effective than traditional manufacturing methods. It minimizes material waste and reduces labor costs due to automated processes. This efficiency can lead to significant cost savings for businesses operating in competitive markets.
3. Speed and Scalability
The speed of production through precision plastic molding makes it ideal for businesses looking to scale up operations. The ability to produce large quantities quickly without sacrificing quality is a game changer in industries such as automotive and electronics.
Precision Plastic Molding Techniques in Detail
Injection Molding
This is one of the most common forms of plastic molding. During injection molding, plastic pellets are heated until they melt and are then injected into a mold. Once cooled, the mold is opened to reveal the finished part. Key advantages of this technique include:
- Ability to produce complex shapes with tight tolerances.
- Short cycle times that enable high-volume production.
- Flexibility in material selection, accommodating various types of plastics.
Blow Molding
Mainly used for creating hollow items such as bottles and containers, blow molding begins with the extrusion of a tube of molten plastic called a parison. Air is then blown into the parison, expanding it to fill the mold. This method is lauded for:
- Producing lightweight containers.
- Efficiency in creating uniform thickness in products.
- Lower material costs for large production runs.
Compression Molding
This technique involves placing plastic material in a heated mold cavity. Pressure is then applied to compress the material and form it into the desired shape. Compression molding is particularly effective for:
- Producing larger parts with consistent quality.
- Manufacturing items that require high levels of durability.
- Reducing overall cycle time when compared to other molding methods.
Extrusion Molding
Different from other methods, extrusion molding transforms plastic into a continuous shape. The process involves forcing melted plastic through a die, creating products like pipes, sheets, and films. Some of its benefits are:
- Continuous production, making it ideal for long parts.
- Ability to incorporate multiple materials in one process.
- Customization options for various thicknesses and lengths.
Applications of Precision Plastic Molding in the Metal Fabrication Sector
The versatility of precision plastic molding extends across various applications within the metal fabrication industry. These applications include:
1. Automotive Components
In automotive manufacturing, precision plastic parts are pivotal. From dashboards to exterior trims, precision molding enables automotive companies to produce lightweight, durable components that contribute to fuel efficiency and vehicle longevity.
2. Electrical and Electronics
Precision plastic parts are critical in the electrical and electronics sectors. They are used to produce housings, connectors, and insulation materials that ensure safety and reliability in electrical devices.
3. Medical Devices
In the medical field, the precision of molded plastic components is vital for the performance and safety of devices. Precision plastic molding is used to manufacture everything from surgical instruments to patient care devices, ensuring that they meet stringent regulatory standards.
Quality Control in Precision Plastic Molding
Quality control is non-negotiable in precision plastic molding. Implementing rigorous quality checks throughout the manufacturing process is essential for maintaining high standards. Effective quality control measures include:
- Material Inspection: Ensuring that the raw materials meet specific quality standards before production.
- Mold Testing: Regular mold maintenance and testing to prevent defects in the final products.
- Process Monitoring: Continuous monitoring of the production process to identify any inconsistencies.
Future Trends in Precision Plastic Molding
The field of precision plastic molding is evolving with advancements in technology. Some future trends to watch for include:
1. Automation and Robotics
Incorporating automation and robotics into precision plastic molding processes will enhance speed, consistency, and safety. This technology will likely reduce labor costs while improving precision and output.
2. Sustainable Materials
As sustainability becomes a more significant concern, the demand for eco-friendly plastics is on the rise. Manufacturers are increasingly looking for biodegradable or recyclable options to meet market demands.
3. Advanced 3D Printing
The advent of 3D printing is reshaping the landscape of precision molding. This technology allows for rapid prototyping and the creation of complex parts that can be customized efficiently.
Conclusion
In conclusion, precision plastic molding plays a critical role in the metal fabrication industry. By understanding the processes and benefits outlined in this article, businesses like deepmould.net can leverage this technique to enhance product quality and operational efficiency. Embracing the advancements and future trends in plastic molding will position companies favorably in an increasingly competitive marketplace.
As industries continue to evolve, staying knowledgeable and adaptable is imperative. Precision plastic molding is not just a method; it is a transformative process that drives innovation and growth in many sectors.